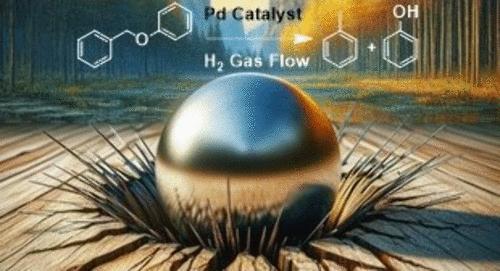
Illustration of a mechanical impact that creates a reactive environment for depolymerization of biomass into value-added chemicals.
Lignin is one of the most plentiful organic polymers on Earth, making up about 20 to 30 percent of the dry mass of wood and other plants.
Despite this abundance, lignin’s complex structure has challenged researchers in breaking it down into useful components that can be used in the sustainable production of chemicals, plastics, and fuels. Therefore, lignin is often discarded as waste during the production of paper and other plant-based products.
However, researchers at the Georgia Institute of Technology have developed an approach that could transform lignin into valuable chemicals more efficiently than ever before.
The researchers published their findings in the journal ACS Sustainable Chemistry & Engineering on using a method known as mechanocatalysis, which uses physical forces, such as vibration or rotation, in a ball mill to drive chemical reactions without the need for solvents, heat, or high pressure.
Carsten Sievers, a professor in Georgia Tech’s School of Chemical and Biomolecular Engineering, explained that the first step in a lignin biorefinery is depolymerization, which breaks lignin down into small molecules.
“Unfortunately, many depolymerization processes require the use of solvents, and separating the products from solvents, catalysts, and contaminants can be complicated, energy intensive, and leave behind waste,” Sievers said.
“One way to reduce the need for these separation steps is to perform lignin depolymerization in a ball mill where collision with steel balls create environments that enable solid-state reactions without the need for solvents or liquid phases.”
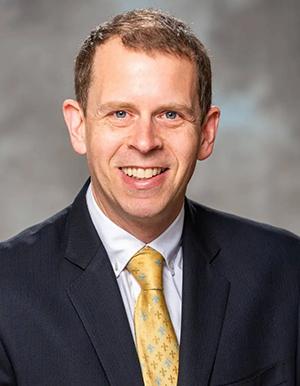
Professor Carsten Sievers
Employing Palladium in Process
Graduate student Erin Phillips (Chemistry), who is co-advised by Professors Sievers and Marta Hatzell, employed palladium catalysts for breaking down lignin’s tough bonds. Palladium particles have the special ability to store hydrogen, making the chemical reactions more efficient.
The researchers collaborated with Eli Stavitski at Brookhaven National Laboratory to use high energy synchrotron x-rays to validate the hypothesis that this way of binding hydrogen prevents it from escaping the impact site of the milling ball. They found their palladium catalysts can break the bonds of lignin model compounds up to 300 times faster than nickel-based catalysts under the same reaction conditions.
“This remarkable increase in efficiency means that the process can produce more phenol and other valuable chemicals in a shorter amount of time, making it a promising approach for large-scale biomass conversion,” Phillips said.
Sievers’ group had previously shown that lignin compounds can be converted with hydrogen and a nickel catalyst in a reaction called hydrogenoloysis. But the time required for that reaction left room for improvement, Hatzell added.
The researchers said their new approach could pave the way for new technologies to harness the untapped potential of lignin and other biomass resources as industries seek out more sustainable and efficient methods for chemical production.
Citation: Erin V. Phillips, Andrew W. Tricker, Eli Stavitski, Marta Hatzell, Carsten Sievers, “Mechanocatalytic Hydrogenolysis of the Lignin Model Dimer Benzyl Phenyl Ether over Supported Palladium Catalysts | ACS Sustainable Chemistry & Engineering,” 2024